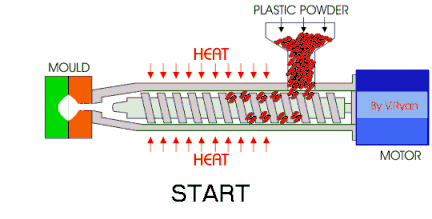
The raw material supplied in granulate form from outside and inside markets is fed to the machine with the systems of automatic loading actuated by vacuum air mounted to the machine. Then, masterbatch is added with the automatic dosage system in the desired quantity to this mixture and so it is provided that the product is coloured.
The raw material smelted electrically in the machines is injected into the volume of the closed mould and time for filling is ensured in such a way that the injected material takes the inner form of the mould. Cooling of the mould and plastic product inside it are made simultaneously by circulation of the water in the pipes, which are machined in the construction stage of the mould. Cooling of the mould reasons also cooling of the injected product. After having completed cooling cycle, the product is taken out from the mould automatically and exposed to examining whether it satisfies quality parameters. Then the approved products by quality control are sent to packing. After that the packed products are stored in the closed warehouse for delivering to customer.
In each stage of the injection moulding process, recycling is possible.