Illustration of the process of the packing design for “powder cleaner” and study of the mould have been indicated in the figures below.
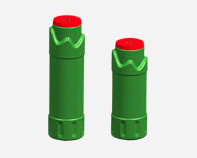
We made the first interviews to obtain the preliminary information related to the design after we received our customer’s request for the design, mould production and bottle production of powder cleaner packing of 500 gr. and 1000 gr. During these interviews, it was understood that the following issues should especially be paid attention.
• The packing will be made as two separate bottles of 500 gr. and 1000 gr.,
• The height of the shelves for these type of products in the stores will be taken into account for the volume determination of the both bottles,
• The bottles will have the maximum label space.
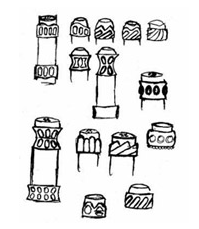
We started with our customer’s own studies. These studies were hand made pattern studies by considering the current applications. We made 3D model studies by considering the production restrictions as well.
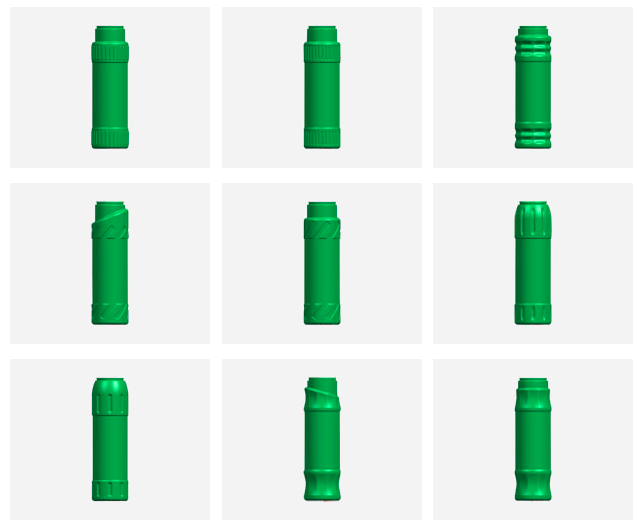
We evaluated these models one by one with our customer during the joint meeting. We found out that the following clauses should be applied as a result of the examination of the usage of product and the status of the competitors and our sales, marketing and service analysis.
• The cap design used in similar products should remain the same but the opportunity for the application of a new cap in the future should be provided,
• The patterns on the bottle should be designed as to prevent dust,
• The wave shape on the brand logo should be used as a pattern on the bottle.
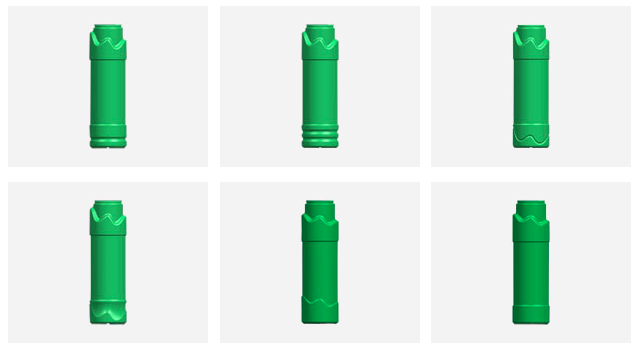
In the next meeting, we eliminated the studies involved usage of the wave shape on the bottle for various reasons. These reasons included visual concerns as well as the necessity of the straight line shape of the label limitation area on the top and bottom sides of the bottle.
As a result, it was decided that the pattern on the top side of the bottle would remain as it is on models on which it is highlighted. The pattern used on the other packing of the company would be used on the bottom side of the bottle. A research should be made to determine how the pattern that is often used in other brands in terms of reminding the product should be used on the product of our customer.
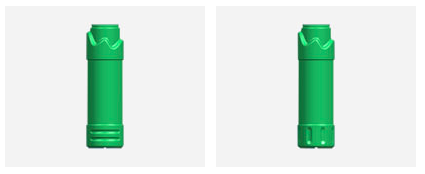
The last two models that we made with these data were presented to our customer. The packing was designed in terms of shape as a result of an evaluation that they made with a more extensive participation.
During the detailed design stage, we implemented the detailed design of the bottles by considering the criteria that we determined on subjects such as the ease of production, suitability with automation and adjustment with the cap. These criteria were as follows:
• The bottom borders of the label should be at the same height as both bottles (small and big) will be labelled on the same automatic labelling line,
• The diameters of both bottles should be the same for the same reason,
• The harmony of the cap and the bottle in terms of shape should be provided and the tap should be closed properly,
• The bottle should not be shaken in vertical position as the filling process will be made automatically on conveyor,
• The patterns should be in a form that will not cause any problems in the mould production.
We produced a prototype of each bottle after the detailed design stage. These prototypes were used in label design, label machinery design, filling and cap closing apparatus design and dimensioning of the cupboard packing in which the product will be placed.
After the prototype approval process, mould design and production were made by answering the following questions;
• How many grams will the bottle weigh?
• What will the daily or annual production quantity be?
• How long will the mould be used for or how many will working-cycle of the mould be operated?
• Which machine will it be operated in?
• What are the possibilities for the usage of automation?
After answering the questions a/m, the production of the moulds has been realised in our plant. Consequently, mass production of the bottles has been continued by using own designed and machined moulds.
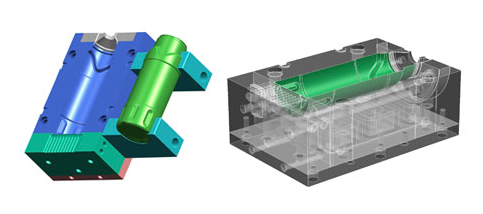